caTEGORIES
Tags
Testing the Performance of Lock Washers in Preventing Bolt Loosening
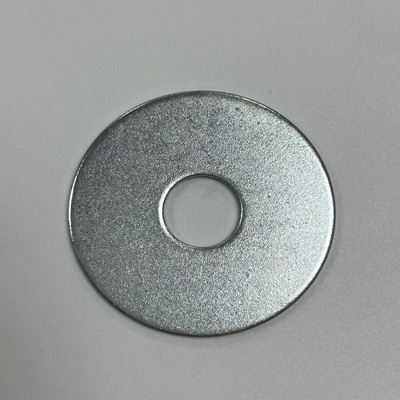
Posted: April 22, 2025
Categories: News
Tags: news
Lock washers are critical for both high-temperature and extreme cycle applications. Real operation of bolt force relaxation is unavoidable, the initial tightening bolt force can only gradually decrease over time.
Factors Influencing Bolt Loosening
The Role of Vibrations in Bolt Loosening
One of the main reasons behind bolted connections loosening is vibrations. Repeated vibrations can cause tension in fasteners to be lost over time, which is a common phenomenon in machinery or structures that are subjected to continuous vibration. This phenomenon arises as a result of the relative motion of the bolt over the surface it secures, it lowers the forces of friction that hold the components in place.
This is especially true in high-vibration environments, such as industrial equipment or automotive applications. This is why special washers, such as lock washers, are widely used to prevent bolts from losing tension and loosening.
Effects of External Forces on Fastener Security
Dynamic loads or impacts are other major external forces that can compromise fastener security. Clamping force can be lost as these forces will move the bolts slightly within their threads. If it is not rectified, over the years, this may lead to total loosening. These external influences can be countered only if the grade used to manufacture these washers is very high.
Material Properties Impacting Washer Performance
Washers perform differently under stress, which is impacted by the different materials used. As an example, they can be corrosion-resistant and durable — making stainless steel washers ideal for harsher environments.
In contrast, carbon steel washers can withstand great tensile forces but may need a protective coating, in order to avoid rust. Choosing the correct material guarantees that the washer is able to resist environmental and mechanical forces from the object it is joining.
Methods for Evaluating Lock Washer Effectiveness
Laboratory Testing Procedures for Lock Washers
Testing in the controlled environment of a laboratory is a starting point to measure the performance of lock washers. The simulation then used a series of tests to replicate real-world conditions, putting the washer through stresses and checking to see how well it was able to maintain tension in the bolts.
Performance metrics such as load retention and loosening resistance are then measured by equipment including tensile strength testers and torsion meters.
Field Testing Scenarios for Real-world Applications
The former one is a good validation but the latter one is a better means of naturally assessing lock washer performance in a natural environment. That means putting washers where they belong—like inside car engines or construction equipment—and watching for the long-term results. Field tests uncover bugs that controlled environments may not have revealed.
Analysis of Lock Washer Designs and Their Performance
Comparison of Split Washers, Tooth Lock Washers, and Wave Washers
Lock washers come in various designs, each tailored for specific applications:
Split Washers: These are among the most common types and work by exerting spring tension against the bolt head and substrate.
Tooth Lock Washers: Featuring serrated edges that grip surfaces tightly, these are ideal for preventing rotation caused by vibrations.
Wave Washers: Designed with a wavy profile, they provide consistent pressure even under fluctuating loads.
Each type has its advantages depending on factors such as load requirements and environmental conditions.
Material Choices and Their Impact on Durability and Performance
The choice of material significantly impacts a washer’s durability and overall performance. For example:
Stainless Steel: Offers superior corrosion resistance but may have lower tensile strength compared to carbon steel.
Carbon Steel: Known for its high strength but requires protective coatings like zinc plating for corrosion resistance.
Brass or Copper: Suitable for electrical applications due to their excellent conductivity.
Selecting the right material ensures compatibility with specific operational demands.
Recommendations for Selecting Lock Washers
Key Considerations When Choosing a Washer for Specific Applications
Choose the appropriate washer for your application to retain your fastener and maintain the working integrity of the system. Choose the washer type according to your project specifications. Considerations including load distribution, vibration resistance, material compatibility, and environmental conditions need to be carefully assessed.
If your application experiences a lot of vibration like in automotive or industrial machinery then go with lock washers with serrated edges or split designs. These washers are designed to resist loosening by gripping the surfaces tightly.
Another factor that needs to be paid attention to is to be careful with sizing. The washer must be fitted closely with the bolt or screw so that loads are transferred through the washer to the substrate with no possibility of local damage.
Highlighting QEWIT Products as Reliable Solutions
For a high-quality source of washers that fulfill every industrial requirement, check out the broad selection of Flat Round Washers DIN 125A in carbon steel and stainless steel, even in zero-rust zinc plating for exceptional rustproofing. Available for various hardness levels (140HV, 200HV, or above), they deliver consistent performance in versatile applications.
They follow international standards which can guarantee that you high quality and traceability of the products. Selecting these washers allows you to improve the performance of your fastening systems while generating powerful customer service.
Enhancing Fastener Security Beyond Lock Washers
Combining Lock Washers with Thread-Locking Adhesives
Washers alone help prevent loosening from vibration or dynamic loads but are most effective if used with a thread-locking adhesion. Made to fill the gaps between the threads, thread-locking adhesives cure into a substantial bonding that prevents movement (even in the most demanding conditions).
In critical high-stress environments with heavy applications such as machinery or aerospace, both lock washers and adhesives are appropriate for high reliability. Avoid ruining joint strength by choosing appropriate adhesives for your materials and operating temperatures.
The Role of Proper Installation Techniques in Preventing Loosening
All washers can fail, even if properly designed if they are not installed correctly. Getting installation right is essential for maximal, long-term performance, please know that proper installation techniques are needed for mitigating fastener loosening over time. It involves tightening bolts with calibrated tools that tighten to specific torque values.
The surface condition also plays a role; clean and dry surfaces provide better frictional contact for lock washers. Additionally, regular maintenance checks can identify potential issues early on, allowing for timely corrective actions. For more products, please visit QEWIT’s website!
FAQs
Q1: What should I keep in mind when selecting a washing machine?
A: Assess load distribution requirements, vibration resistance, compatibility with materials, environmental conditions and sizing suitability according to your application.
Q2: How do thread-locking adhesives work with lock washers?
A: They act like glue between the threads to bond the fastener for movement under severe conditions, making fasteners more reliable in general.
Q3: Would proper installation make any difference in performance?
A: Yes, proper installation leads to optimal performance as it maintains the right torque values and provides better surface material frictional contact.