caTEGORIES
Tags
How to Ensure Safety When Working with Self-Drilling Screws
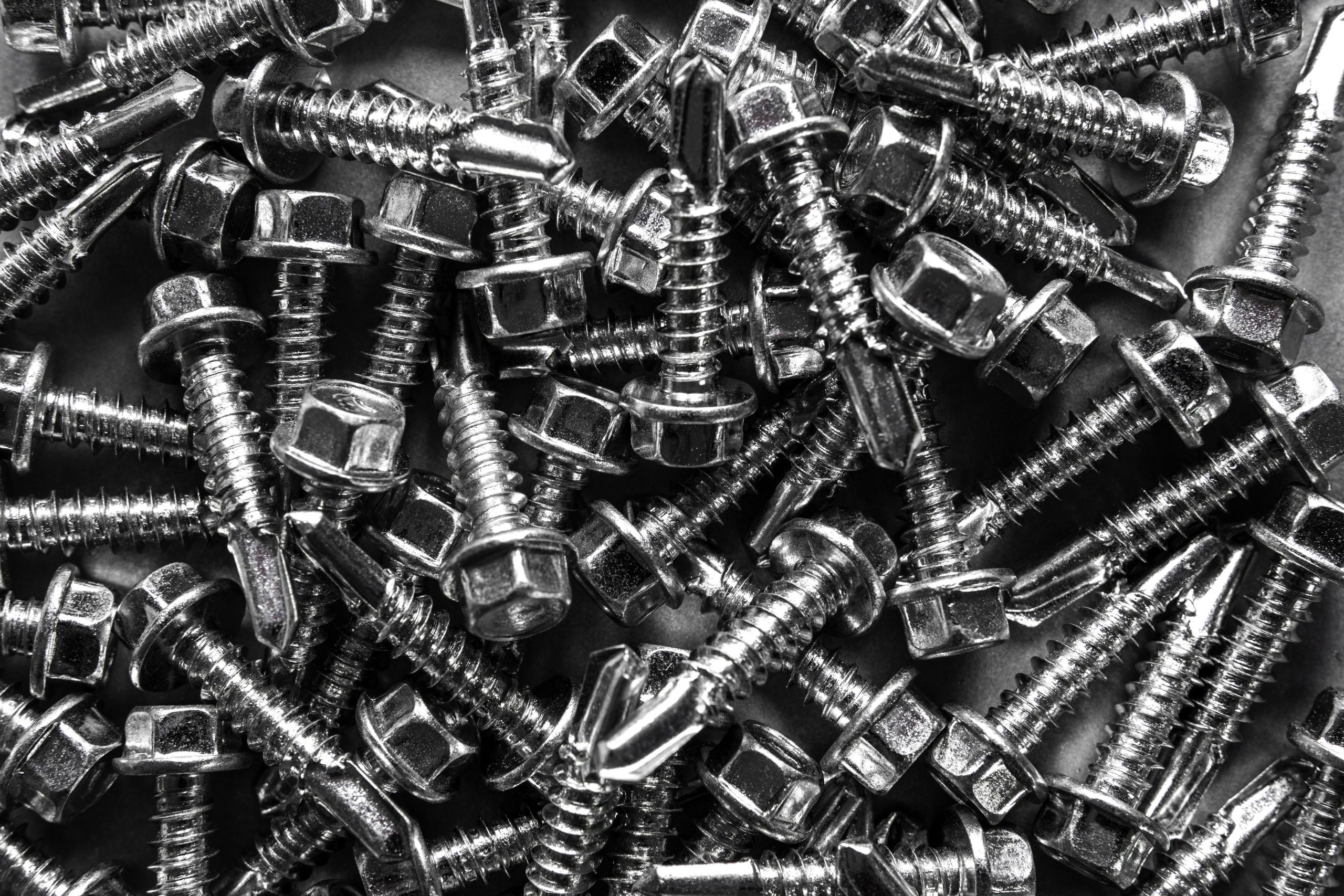
Posted: April 24, 2025
Categories: News
Tags: news
Some safety tips used while working with self-drilling screws have been given below. Do not forget to follow all safety protocols and precautions relevant to the specific task. Safety training and awareness should be promoted regularly for the workplace to remain safe.
Preparation Before Using Self-Drilling Screws
Selecting the Appropriate Tools for Installation
Depending on the different kinds of tools we use on other materials, one of the most significant steps involved with preparing self-drilling screws is the installation of the right tools. The right equipment matters a lot in terms of how accurate your installation is. You need a power drill to manage the torque and avoid damaging the screw or material, so you want one that is high-quality and has adjustable speed settings. Also, check to see if you have the appropriate drill bit to match the diameter of the self-drilling screws.
Inspecting the Work Environment
Check your immediate surroundings before you start any installation. Make sure that the surface you want to use self-drilling screws on is clean and free from dirt or contaminants. This is an important step because dirt or grease can affect the ability of the screw to penetrate the materials right.
Choosing the Correct Type of Self-Drilling Screw
The uniqueness of each self-drilling screw type is critical for the right final reliable installation. Keep in mind elements like material thickness, environmental exposure, and load demands. As an example hex screws with bright zinc-plated finish are resistant to corrosion in humid conditions and stainless steel ones are more effective in extraordinarily corrosive environments.
Safety Measures During Installation
Proper Handling Techniques for Self-Drilling Screws
By using self-drilling screws with care, the chances of anyone getting hurt or any material that is being used to get damaged during installation will be minimal. Always wear the correct personal protective equipment (PPE) such as gloves, and safety goggles to protect against sharp edges or debris flying through the air.
When inserting screws into a power drill chuck, ensure they are securely fastened to prevent wobbling during operation. Loose screws can lead to uneven drilling and potential accidents.
Maintaining Stability During Drilling
Ensuring stability during the drilling prevents accidents including misalignment or stripped threads. Clamp the material being drilled down securely so that it does not move when being drilled. Also, maintain a steady pressure against the power drill, but do not push down; the self-drilling screw is designed to do its job smoothly.
Also, consistent pressure is needed on the power drill, but do not apply excessive force; the self-drilling screw is designed to self-drill without excessive force being applied to the power drill.
Keep your work environment bright and organized so that distractions that can hinder your focus and stability are minimized. Ladders and scaffolding with anti-slip features must be used, especially when working on vertical and overhead installation.
Managing Power Tool Operations Safely
Operating power tools safely requires adherence to best practices and manufacturer guidelines. Start by inspecting your power drill for any signs of wear or malfunction before use. Faulty equipment increases risks significantly during installation tasks.
Adjust your drill’s speed settings based on material density; slower speeds are preferable for harder materials to prevent overheating or damage to both the screw and surface. Always unplug power tools when changing bits or performing maintenance tasks.
Post-Installation Safety Practices
Inspecting Installed Screws for Proper Placement
Once the self-drilling screws are installed, an inspection is really important for safety and durability. Verify that every single screw is aligned well and your screw ends are not cut too deep. Even improperly aligned screws can weaken the integrity of your project, and screws needing too much torque can damage the material or weaken the grip of the fastener. To ensure the screws are fastened to factory specifications, use tools such as torque wrenches.
For variations in functionality, you can use any of the High-performance application products such as Hexagon Head Set Screws DIN 933. They are very high tension, exerting a high holding power and are corrosive resistant, making them well-equipped for the toughest environments.
They meet international standards, making them reliable and safe in different installations. High compliance with international standards makes them suitable for any installation where proven reliability and safety are required.
Cleaning and Storing Tools After Use
Taking care of your tools after you install them is essential to ensuring they work right and last as long as possible. Purge any tools, including power drills and bits of debris or residue that may impede the tool from operating properly.
Keep them neatly stored in a dry area to avoid rust or damage. Maintenance not only prolongs the life of your equipment but also helps you achieve steady performance in your future projects.
Recommendations for Long-Term Safety Practices
Regular Maintenance Checks on Installed Screws
It is important to regularly inspect structures that are fixed with self-drilling screws for safety in the long run. Check fasteners for wear corrosion or loosening at regular intervals, fasteners may have their integrity compromised due to environmental factors, such as moisture or temperature changes, in the long run. You should also replace every damaged or corroded screw to ensure the structural stability of your building.
Choose a fastener with superior finishes for applications that are exposed to extreme conditions like Pan Head Recessed Machine Screws DIN 7985. Bright zinc-plated screws have great corrosion resistance, making them perfect for outdoor or high-humidity locations.
Continuous Training on Safe Installation Techniques
Keeping Up-to-Date with Industry Standards
As the fastening operation is an essential part of the workflow from manufacturing to vehicle tooling where safety is an utmost concern, one must keep themselves updated on the standards of the particular industry. Fasteners are guided by standards such as DIN933 or ISO4017, which include direction on material, mechanical properties, and dimensional tolerances. Following these standards helps maintain interchangeability and consistency in many applications.
Suppliers specializing in industrial consumables often provide resources to help professionals stay updated on these standards. Leveraging such expertise can enhance your knowledge and application of safe installation practices.
Leveraging QEWIT Resources for Expert Guidance
Contact to receive professional assistance on fastening solutions from a trusted supplier such as QEWIT. A company with a history of high-quality fasteners since 2004, they provide their products for every need in the sector. The technical support services also grant businesses access to high-end testing facilities, including tensile strength testers and plating thickness testers, to keep the products in accordance with international standards.
By utilizing resources from experienced suppliers, you can optimize your fastening operations while adhering to best practices for safety and efficiency.
FAQs
Q1: How often should I inspect self-drilling screws that were installed?
A: Inspect annually or more often if in corrosive or high-use settings.
Q2: What can I do if any screw goes loose after some time?
A: As appropriate, torque it after reinstallation with a torque ranch; not an option, replace with a new screw that meets original specifications.
Q3: What tools do you recommend for replacing screws in the assembly?
A: For tight tolerances, use torque wrenches for accurate tightening; for corrosion resistance, use drill bits that are compatible with the type of screw being replaced or adjusted.