caTEGORIES
Tags
Exploring the Functional Differences Between Heli-Coil and Threaded Inserts
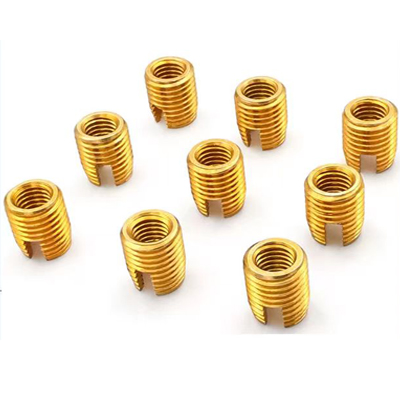
Posted: April 10, 2025
Categories: News
Tags: news
The uses and advantages of these two types of threaded inserts differ in their functions, and when considering what to use, let us explore their functional distinctions. Although both types of inserts enable strong and durable threads, their particular designs and applications are not suitable for all types of materials.
Characteristics of Heli-Coil Inserts
What Makes Heli-Coil Inserts Unique in Design?
Heli-Coli inserts are precision-engineered components for robust and reliable threaded connections for various applications. They have a helical coil design which distributes load evenly along the threads. Alongside this feature, it not only strengthens the connection but also prevents unnecessary friction and wear.
The helical style also keeps the insert mechanically locked in place under high vibration or any other stress. Heli-Coil inserts increase the effective bearing surface, improving the wear life of the threaded connection.
Are Heli-Coil Inserts Durable and Long-Lasting?
Their strength lies in the materials Heli-Coil inserts are made. Usually crafted using high-quality stainless steel, these inserts are corrosion-resistant and wear-resistant, allowing them to shine even in hostile environments. Characteristics of stainless steel will guarantee that under extreme mechanical loads, the integrity of the inserts will be intact.
The durability of Heli-Coil inserts is further enhanced by their ability to distribute stress evenly across the threads. This reduces localized stress concentrations that could otherwise lead to premature failure.
Where Do Heli-Coil Inserts Excel?
Heli-Coil inserts shine in applications where thread repair or reinforcement is necessary. Widespread use of these materials is expected for aerospace, automotive, and electronics industries, for example, strong permanent joining with lightweight materials.
They are also used extensively in MRO situations where the need to restore damaged threads is paramount. They are also a go-to option for technicians aiming to maximize equipment service life with little downtime because of how simple they are to install.
Characteristics of Threaded Inserts
What Are the Structural Variants of Threaded Inserts?
There are several different structural designs for threaded inserts, each dependent on its application. The most typical options include self-tapping inserts, press-fit inserts, and heat-set inserts. Self-tapping inserts cut their threads as they are installed, so they are perfect for plastics or soft metals.
How Strong Are Threaded Inserts Over Time?
Material strength of a threaded insert is critical. They can be made from carbon steel, stainless steel, brass or even zinc alloys to achieve various levels of strength and corrosion resistance. Conversely, for its high tensile strength and resistance to environmental degradation, stainless steel threaded inserts are preferred.
The fact that they are corrosion and wear-resistant makes threaded inserts a fantastic solution for indoor and outdoor applications where there is exposure to moisture or chemicals. These act as rust and wear protection, so threaded inserts can be used for both indoor and outdoor applications that may be exposed to moisture or chemicals.
What Are Common Applications for Threaded Inserts?
Because of their versatility, threaded inserts are used throughout various sectors. Heat-set variants induce hard bonds between thermoplastic elements in plastics manufacturing.
Industrial machinery often employs threaded inserts for mounting heavy components securely without compromising structural integrity. Additionally, they are indispensable in consumer electronics for creating reliable connections within compact devices.
Comparing Performance Between Heli-Coil and Threaded Inserts
Which Has Better Load-Bearing Capacity?
Both Heli-Coil and threaded inserts offer excellent load-bearing capabilities, but they are best in different applications—let’s take a look at the two side by side. The helical Heli-Coil stacked design, which sits within the host hole, ensures a constant load distribution across threads, making it well suited for demanding, high-stress locations, such as those found in aerospace applications.
However, thicker-walled threaded inserts could also provide better load-bearing capacity in wood or plastic materials, due to their larger contact area with the surrounding material.
How Do They Resist Wear and Corrosion?
Wear and corrosion resistance are mostly a function of the material and overlay. Both varieties are frequently used in stainless steel because of their good anti-corrosion properties, but added finishes such as zinc plating or galvanization can improve protection further.
Unless you are coating some brass or zinc alloy threaded insert to resist the environment, you have to know that the stainless steel construction of Heli-Coil will resist better intrinsically.
How Easy Are They To Install And Maintain?
The installation processes are quite different for the two types. Heli-Coil installs normally need to be pre-drilled and then threaded using specific devices to prepare for the coils to be entered a prolonged process that takes skill but provides amazing results once done.
Depending on the type of threaded insert being installed (self-tapping vs. press-fit), threaded inserts also provide installation methods that can be more straightforward—self-tapping variants eliminate the need for pre-drilling entirely, while press-fit models merely call for proper alignment during insertion.
Specific Recommendations for QEWIT Products
How Does QEWIT Revolutionize Threaded Inserts?
An important component in many industries, threaded inserts provide an easy and cost-effective way to create a robust connection. Leading the change, QEWIT has set new product standards by providing sophisticated solutions to various applications. With a catalog of 30,000+ product lines from ISO-certified processes, this company is synonymous with high quality and performance.
The threaded inserts offered include self-tapping, press-fit, and heat-set variants, each designed to meet specific industry requirements. Besides, QEWIT has test facilities to ensure the quality.
How QEWIT’s Technology Enhances Insert Performance
The reliability of threaded inserts is highly farmed on material and precision. They use only the best materials, including stainless steel, carbon steel, brass, and alloys, to make sure that the product is durable and will not wear out or corrode quickly.
Their advanced manufacturing capabilities include forging, machining, and punching techniques that enable customization according to precise specifications. This ensures every threaded insert is optimized for its intended purpose.
Selecting the Right Insert for Specialized Applications
What Factors Should You Consider When Choosing Between Heli-Coil and Threaded Inserts?
Some of the factors affecting the selection of Heli-Coil versus threaded inserts are the type of material, load-bearing requirements and environmental settings. The helical coil structure of Heli-Coil inserts disperses stress evenly over threads.
In contrast, threaded inserts allow for dynamic designs such as self-tapping or press-fit designs. Suitable for use with softer materials such as wood or plastics, where wider contact areas provide better load-bearing capacity. However, the ultimate decision depends on the particulars of your project.
Which Industries Benefit Most from These Solutions?
Both Heli-Coil and threaded inserts serve various industries but excel in different scenarios:
Aerospace: Heli-Coil’s helical design ensures reliability under extreme mechanical loads.
Automotive: Threaded inserts provide durable connections in lightweight materials like magnesium.
Electronics: Heat-set variants create robust bonds within compact devices.
Woodworking: Threaded inserts withstand repeated assembly without degrading structural integrity.
Industries requiring precision and durability can rely on these solutions to meet stringent performance standards while reducing maintenance costs over time.
FAQs
Q1: How do QEWIT threaded inserts differ from the rest?
A: They use high-grade materials such as stainless steel and import good quality, like zinc plating, however, it does not have the combination of being both durable and very resistant to corrosion.
Q2: Can I customize threaded inserts for unique applications?
A: Yes, bespoke manufacturing services allow customization based on drawings or samples, with certifications like 3.1 or PPAP available upon request.
Q3: Is there an option for quick installation?
A: Self-tap threaded inserts require no pre-drilling, which can be an instant advantage if time to market is critical in the production of parts.