caTEGORIES
Tags
Fatigue and Stress Corrosion in Washers: Expert-Level Insights
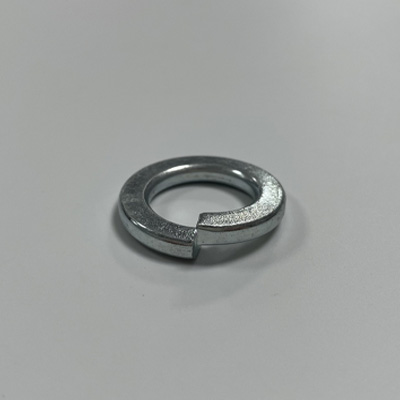
Posted: May 02, 2025
Categories: News
Tags: news
Fatigue and stress corrosion are two critical factors that can significantly impact the performance and lifespan of washers. Hence, fatigue and stress corrosion are important to study to avoid failure of washers and to be able to develop more durable and reliable ones.
Fatigue Failure in Washers
Mechanisms of Fatigue in Washer Applications
In this regard, repeated cyclic loading over time leads to the phenomenon of fatigue failure in washers through the gradual deterioration of the material. Such behaviors are especially important in applications where washers experience dynamic forces such as vibrations or varying mechanical loads.
The fatigue mechanism starts from the initiation of tiny cracks on the surface of the washer. Fatigue resistance can be improved in high-grade fasteners & washers, those made of stainless steel or carbon steel with a hardness of 200HV or higher.
Factors Contributing to Fatigue in Washers
Fatigue failure in washers is affected by a number of different aspects such as material properties, design features and operating conditions. The material itself has a significant impact; higher-strength alloys usually perform better than softer materials in fatigue resistance. Surface finish is also a key parameter — rough surfaces can worsen stress concentrations and lead to crack initiation.
Environmental conditions such as temperature fluctuations and exposure to corrosive elements also contribute significantly to fatigue. Proper installation techniques further mitigate fatigue risks by ensuring even load distribution across the washer’s surface.
Stress Corrosion Cracking in Washers
Conditions Leading to Stress Corrosion Cracking
The combination of tensile stress and a corrosive environment is a failure mechanism of concern known as stress corrosion cracking (SCC). SCC in washers is usually under chemical agents and mechanical stress. While this type of failure is insidious since the failure can occur at levels of stress less than the yield strength of the material.
However, washers manufactured from stainless steel quality types such as A2-70 or A4-70 will also resist SCC due to their inherent corrosion-resistant qualities. They are especially useful in applications that involve chlorides or other extreme chemicals. By adding certain elements, such as chromium, they gain the capability of developing a protective oxide layer.
Role of Environmental Factors in Stress Corrosion of Washers
Environmental aspects are considered to be triggering factors in accelerating SCC in washers. Humidity, salt water and acidic or alkaline conditions can degrade the material of the washer.
This is countered to a degree through surface finishes: hot-dipped galvanization (HDG) or zinc flake coatings are specified to make them more corrosion-resistant.
Such component is provided with extra resistance from external environmental damage using treatment techniques like zinc plating or HDG.
Mitigation Strategies for Fatigue and Stress Corrosion in Washers
Mitigation strategies for fatigue and stress corrosion in washers involve understanding the factors that influence these issues and implementing appropriate countermeasures.
Material Selection for Enhanced Performance
High-Performance Alloys for Fatigue Resistance
Because of this, selecting appropriate material choice is essential to prevent fatigue failure in washers. Cyclic loading has great resistance with high-performance alloys. Such materials are designed to withstand dynamic loads without microcrack growth.
The resistance to fatigue cycle failures makes it an obvious choice in those environments that are either subject to impacts or fatigue cycles (stainless steels), where its toughness and ability to develop a protective oxide layer will prove advantageous. These alloys are especially effective in applications where long-term durability is required, such as automotive or aerospace industries.
Corrosion-Resistant Coatings and Their Applications
Prolonged durability of washers can be ensured by protective coatings, which ultimately protect these fasteners from environmental factors affecting the high rate of wear and tear.
Zinc plating, hot-dipped galvanization (HDG) and zinc flake coatings are common post-coating finishes for improved corrosion performance. Coupling high-performance materials with proprietary coatings will make washers significantly more robust in aggressive environments.
Design Considerations for Reducing Failure Risks
Optimizing Washer Geometry to Minimize Stress Concentration
It is the geometry of the washer that dictates the amount of mechanical stresses a washer can remain in place. Design with smooth edges and surfaces can distribute the stress evenly to the washer surface; therefore, rounded edges and smooth surfaces are key design features for washers.
Any sharp corner or irregularity in the material will act as a concentrator of stress and will result in the initiation of cracks in cyclic loads. Engineering simulation and CAD tools help together in simulating the stress and thus the functionality by varying the geometry of the washer.
Load Distribution Techniques to Extend Washer Lifespan
Another crucial one is how they disperse the load correctly in order not to increase the failure risks of washers. The lock washer and spring washer are set between bolting joint surfaces to keep even pressure to prevent local stress.
Furthermore, using washers with built-in serrations, as seen with flange nuts, creates a locking effect that grips the underlying surface of the bolt head or nut and improves resistance to loosening from vibrations.
Recommendations Based on QEWIT Products for Superior Washer Performance
QEWIT’s High-Strength Washers for Fatigue-Prone Environments
Products like Flat Round Washers DIN 125A are geared to help solve the problem of fatigue failure owing to their compliance with stringent standards coupled with high endurance. These types of washers can be made with carbon steels as well as stainless steels that allow various industrial applications.
These parts are made to handle dynamic loads coming on them with ease and a hardness rating of 140HV, 200HV, or higher. Aside from their natural corrosion resistance, their galvanized finish takes it a step further, making them suitable for more hostile environments.
Corrosion-Resistant Solutions from QEWIT for Challenging Conditions
If the application is exposed to harsh chemicals or high humidity, corrosion-resistant solutions are necessary. Products having surface treatments such as zinc plating or HDG are designed to protect against environmental deterioration.
For instance, Hexagon Serrated Flange Nuts DIN 6923 have serrated flanges that function as integrated washers which maximize vibration resistance and provide optimal protection against corrosion. Not only do these innovations come up to industry standards, but they exceed beyond imagination on a single section of quality and performance.
By leveraging advanced materials and designs tailored to specific operational demands, you can achieve optimal results while mitigating common failure modes associated with QEWIT‘s products.
FAQs
Q1: What are the best materials for washers in terms of fatigue resistance?
A: High-strength alloys such as stainless steel grades A2-70 or A4-70 and hardened carbon steel (200HV +) provide excellent fatigue resistance.
Q2: What makes it durable with protective coatings?
A: With total coatings such as zinc plating or clever degassing, moisture and also chemical substances are stopped from reaching the steel under the majority of biome-controlled problems, making use of the desirable convenience of growth.
Q3: Which design features reduce the stress concentration of washers?
A: Rounded edges, smooth surfaces, and optimized geometries help get stress distributed evenly throughout the surface of the washer, minimizing the chance of crack promotion.