caTEGORIES
Tags
Choosing Threaded Inserts: Key Factors for Expert Decision-Making
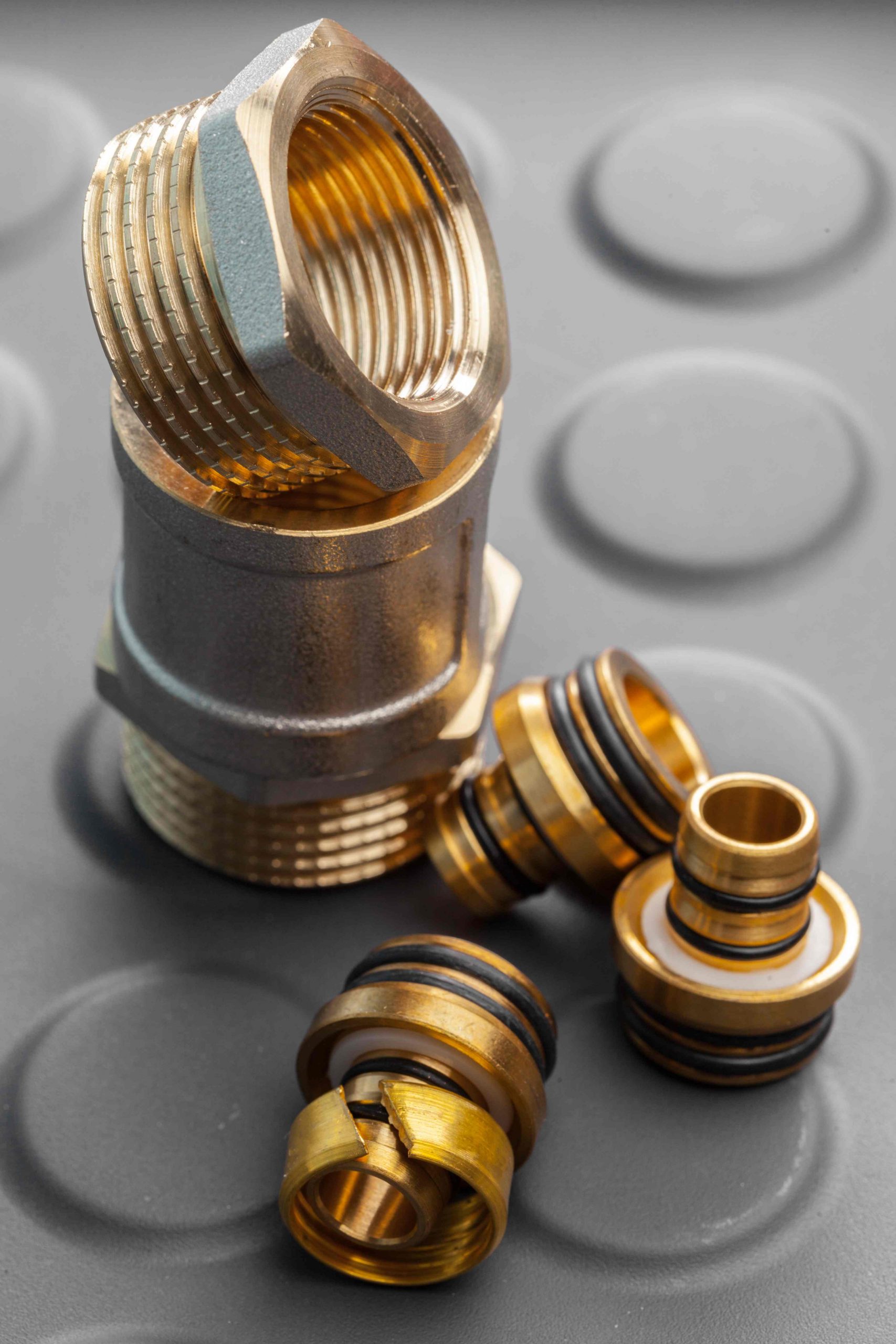
Posted: April 15, 2025
Categories: News
Tags: news
Making the right choice of threaded inserts requires some thought and consideration to make an expert decision. Careful consideration of those factors should help you find the right threaded insert to reliably address your specific application. By understanding the factors that are relevant, you can determine which type of threaded insert is best for your application, allowing for reliable performance.
Material Selection for Threaded Inserts
Evaluating Insert Materials for Specific Applications
The material of the threaded insert is important when selecting the right one for your application. Threaded inserts are made of different materials such as brass, stainless steel, aluminum, and carbon steel. All materials have their benefits to the needs of the operation. Different materials have their benefits depending on the operational demands.
Stainless steel or brass inserts are perfect for applications where corrosion resistance is vital, as their resistance to oxidation and rust makes them ideal where corrosion resistance is a primary concern. Brass, especially, offers good machinability and is extensively used in electrical and plumbing applications.
Aluminum inserts are, in contrast, very light and ideal for instances in which weight reduction is necessary, like aerospace parts. In heavy-duty industrial applications, carbon steel inserts are preferred because they provide high strength and durability.
Matching Insert Materials with Host Materials
Another very important factor is the compatibility of the threaded insert material with the host material. So when using poor matching materials, it may cause galvanic corrosion or structural integrity of the hardware. For example, brass inserts mate best with softwoods or plastics thanks to their softer tendencies and overall ease of installation. Stainless steel inserts will do well in metals such as aluminum or steel because they have similar characteristics.
However, host materials such as thermoplastics also need inserts that can withstand repeated usage stress without deformation. In thermoplastic applications, brass heat-set inserts are highly effective because they form a very strong bond when seated and heated into place.
Types of Threaded Inserts and Their Applications
Press-In Inserts for High-Load Applications
Press-fit inserts are used in applications, such as that require heavy loads to be borne. Inserts are often installed by being press-fit into the pre-drilled holes of the host material. Friction or knurled surfaces are used to hold them in place.
Such inserts are widely employed in metalworking sectors that demand secure fastening. A great example would be carbon steel press-in inserts that are perfect where tensile strength and durability are necessary in automotive manufacturing or heavy machinery assembly.
Heat-Set Inserts for Thermoplastics
Heat-set inserts are intended for thermoplastic materials. They are heated during installation so that they melt the plastic surrounding them and they are embedded in the host material as it solidifies.
Metal inserts like brass are a common choice for heat-set plastic inserts because brass is a good thermal conductor that does not deform easily when heated. Such features are perfect for application in electronics enclosures or consumer gadgets needing accuracy in fastening.
Self-Tapping Inserts for Soft Materials
Conversely, self-tapping inserts create their threads in softer host materials like wood or soft plastics when inserted. This means no pre-threading steps are required, and everything can be built to tight tolerances inside the host material.
These inserts commonly come with external threads, which allow for fast installation while retaining high pull-out resistance. Aluminum self-tapping inserts are especially beneficial in lightweight assemblies such as furniture for office assembly and portable equipment.
Installation Methods and Tools
Manual Installation Techniques
With manual installation methods, you use hand tools such as screwdrivers or insertion wrenches to insert thoughtful inserts placed into pre-drilled holes. With this approach, it is best for small projects, or if you have to repair and precision is not important, but reliability remains important.
For example, when using softwoods or plastics, brass self-tapping inserts are best installed manually for minimal host damage when fitted securely. Generally, when inserting into softwoods or plastics, it is best to do so without the use of a drill, as manufacturing comes with the least amount of damage to the host material while providing a secure fit.
Automated Installation Solutions
In industrial settings where efficiency is crucial, automated installation solutions play an important role. These methods utilize specialized machinery capable of inserting threaded components at high speed without compromising accuracy.
While this can be a time-consuming process as each install must be fully inspected, in high-volume use cases for threaded insert installations across a number of units, automated systems have a significant advantage. As an example, insertion tools affixed to robotic arms can conveniently insert press-in or heat-set inserts into metal assemblies or thermoplastic parts.
Performance Considerations for Threaded Inserts
Load-Bearing Capacity and Durability
When choosing a threaded insert, it is all about load-bearing capacity and durability. Threaded inserts are designed to be used under high stress and repeated use conditions to enable a strong connection with various materials. The insert’s ability to support loads relies heavily on the composition of the material from which it is made.
Besides, the insert design affects the performance under load. Knurled surfaces or helical grooves further increase the grip in the host material, reducing pull-out failure. These designs are particularly effective when used as metal and general-purpose inserts in dense plastics in applications requiring strong fastening.
Another factor is durability, which is vital for environments where the insert will eventually come under wear and tear. Stainless steel inserts provide extraordinary robustness when it comes to corrosion and mechanical wear, making them ideal for long-term applications under difficult conditions.
Corrosion Resistance in Varied Environments
Moisture, chemicals, or extreme temperatures can expose the insert to conditions that would accelerate corrosion or weaken the integrity of the insert. The materials they choose come with greater corrosion resistance, such as stainless steel and brass.
An insert with a protective coating can even be selected to improve environmental resistance for specialized needs. Zinc-plated and hot-dipped galvanized options offer additional protection against rust and chemical exposure.
Recommendations Based on QEWIT Products
QEWIT Solutions for High-Strength Requirements
In case you are working on a project that requires high-strength fasteners able to withstand heavy stress, then you may check out the threaded inserts provided by QEWIT. QEWIT consists of a wide variety of fasteners available in carbon steel, stainless steel, brass, and alloys. Threaded inserts are manufactured to specifications that set high-quality standards while also maintaining high load-bearing abilities.
With ISO9001-certified processes and advanced testing facilities like tensile strength testers and proof load testers, you can be assured of consistent product reliability.
Customizable Options from QEWIT for Specialized Needs
Standard products will not necessarily meet the needs of every application. When that happens, you need customized solutions that are relevant to the specific operational conditions. QEWIT specializes in non-standard fastening products customized to be made according to customer drawings or samples.
They not only have a manufacturing ability but also provide pre-production samples on request. These are examples of additional services that guarantee every lot meets specific requirements before being shipped out. This level of precision ensures that your custom threaded inserts will fit perfectly into your project and perform as intended.
FAQs
Q1: How do I determine the right material for a threaded insert?
A: Assess factors like load requirements, environmental exposure (e.g., moisture or chemicals), and compatibility with host materials when selecting an insert material.
Q2: Why use a stainless-steel threaded insert?
A: Stainless steel is highly corrosion resistant, durable and is ideal for harsh environments, including marine or industrial locations
Q3: Do I need custom dimensions for threaded inserts?
A: Yes, QEWIT is providing fully customizable services, even to manufacture non-standard threaded inserts, so a little input is required from the customer and they’ll work from there.